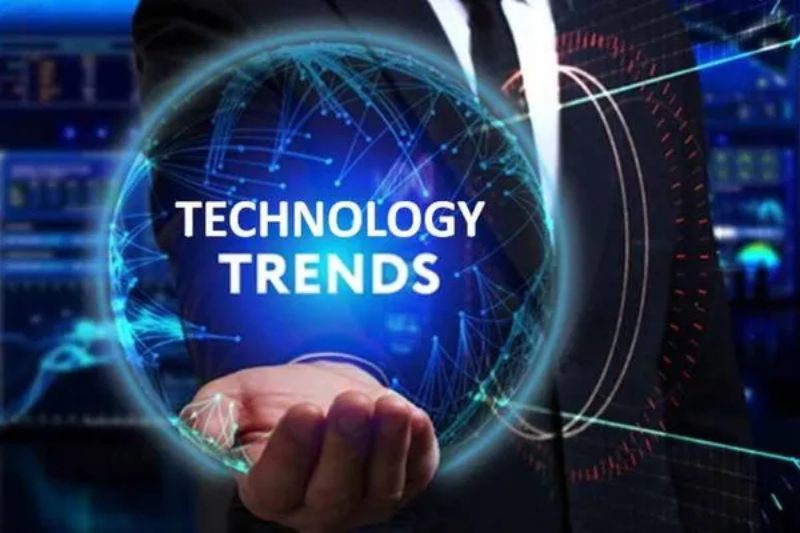
The Top 5 Tech Trends in Construction to Keep an Eye on in 2024
- Technology
- January 5, 2024
The numerous difficulties that the construction industry faces have spawned creativity and a plethora of novel—and not so novel—ideas about how technology may assist in resolving issues faced by the sector from trailblazers to tech companies and their supporters.
Due to a lack of skilled labor and a persistent struggle for increased efficiency, robotics, automation, and artificial intelligence (AI) are starting to emerge as viable ways to help close the productivity gap in the construction industry.
Many understand from personal experience that technology is the only way to address the need for higher-quality, more efficient construction. Additionally, the pressing need to decarbonize the building sector due to the climate emergency facing our planet necessitates the use of technology that allows us to measure our impact.
All of this means that the greatest industry in the world is going through a tremendously exciting, fast-paced, and unexplored phase. These are the top five construction tech trends to watch in 2024, listed in no particular order.
1. The use of artificial intelligence
Artificial intelligence (AI) has started to impact many areas of life in the past year as rules catch up, but if you thought AI was limited to making the Pope seem better, think again.
These days, technology is also reshaping the building and architecture industries. A vast range of AI-generated designs are starting to surface, a trend that is apparently both admired and hated in equal measure. These designs are created by professionals in the field of architecture as well as amateurs and digital artists.
Even Zaha Hadid Architects has acknowledged that the firm uses technology for some of its projects even at the early stages of design and brainstorming.
Early in the design process, ideas are generated using software such as DALL-E 2 and Midjourney, some of which are then turned into 3D models.
Artificial Intelligence (AI) has been included in “predictive design” technologies for a while now. It may be used in engineering to create structures-optimizing algorithms. China’s Shanghai Tower was designed with maximum efficiency through the application of machine learning in its finite element modeling.
This rapidly evolving field is anticipated to accelerate once more in 2024, bringing with it new opportunities, difficulties, and a healthy dose of controversy for the sector.
2. Online Cooperation
In 2024, the construction sector will be even more interconnected because to the development of digital collaboration tools like Bluebeam Revu, Cloud, and Studio.
Hundreds of printed drawings had to be sent across teams every time revisions were made, making it difficult to keep track of progress on a work site.
When a single document is exchanged over the cloud from the architect’s office to the construction crews on the ground, products such as those offered by Bluebeam create an effective single source of truth. This ensures that the correct plans and technical sheets, complete with markups and updated versions, are being viewed by all.
Digital collaboration solutions like these are becoming indispensable in an era where teams are dispersed across several projects and where working remotely or remotely via hybrid means has remained the norm.
It’s the kind of feature that’s simple to take for granted, yet Bluebeam is assisting in establishing a new benchmark for the sector that, by 2024, may well prove to be its very cornerstone.
3. The use of 3D printing
Although it may not be the newest technology on this list, 3D printing may have at last found a home in the toolkit of the building sector by 2024.
ICON, a 3D printing company, is one convincing piece of evidence in the pudding. The company started building 100 new homes in Texas in 2023 and has big plans to expand.
A house’s shell can be printed in roughly two weeks, after which windows, doors, and roofing are added.
According to recent studies, 3D printing may be 25.4% less expensive than conventional techniques. Given the skyrocketing costs of labor and materials, these kinds of savings are starting to make 3D printing a more attractive alternative.
However, there are other reasons why this technology is exploding. NASA’s Project Artemis has selected ICON to construct lunar dwellings, with the first units expected to land by 2030.
4. Automation
There is pressure on the construction industry to increase productivity due to high inflation and a skills shortage. Robotics and automation are experiencing tremendous innovation due to this dynamic, and as 2024 approaches, these fields are anticipated to see further growth.
Modern construction techniques, such as off-site manufacturing, make it possible to choose building components from a pre-defined kit of parts and have them precisely prefabricated under controlled conditions before they are simply put on site. This improves quality and saves time and money.
Regarding robots, the humanoid Atlas robot from Boston Dynamics may be useful for moving large objects around construction sites and possibly for exploring regions that are too hazardous for people to enter, while Australian company FBR’s Hadrian X is refining its house-building skills.
Even if it all seems incredibly implausible and futuristic, the potential of some labor parts being automated by robotics is absolutely unavoidable as the construction industry’s skills issue comes to a head in the coming years (about 41% of the existing workforce is expected to retire by 2041).
5. Virtual Replicas
Last but not least, there is a technology that may be able to assist with the climate emergency, which is currently our generation’s most pressing issue.
Thirty percent of carbon emissions come from the built environment. Therefore, in order to mitigate the effects of climate change, we must ensure that our buildings are designed and run as effectively as possible. Digital twin technology can help with this.
Digital twins, which serve as virtual representations of actual constructed assets and are filled with historical and real-time data from sensors and technology inside a building, allow us to track energy consumption and cut down on waste. Scaling such data allows it to contribute to decision-making for entire campuses, districts, or even cities.
At least in the UK, the industry appears to be transitioning from a phase of digital twin adoption that was characterized by hype and buzzwords to a more mature stage of beneficial implementation and upskilling.